Tension and pressure, tears and creeps. The Wingnut Test Facility (WTF) gets dope-slapped in our latest round of experiments.
The Wingnut Test Facility, or WTF, conducting new PSA tape testing in preparation for the NESEA BE14 Demonstration Stages, learned how half a dozen or so tapes are performing on half a dozen different substrates. We also learned, to our surprise, that pressure, or “bellowing,” may not be as important a factor as the wing nuts first thought. (For background on WTF and its prior tape tests, see “Shocking Truth About Tapes Emerges from Wingnut Test Facility!”, and to find BuildingGreen-approved tapes, see our guide to Weather & Air Barrier products.)
Dave Gauthier and I decided two things at the end of our last round of testing:
- We needed a more-realistic, longer-term, “straight-pull” tension test.
- We needed a test that reflected the “bellowing” pressures that tapes see in real installations, driven by wind events.
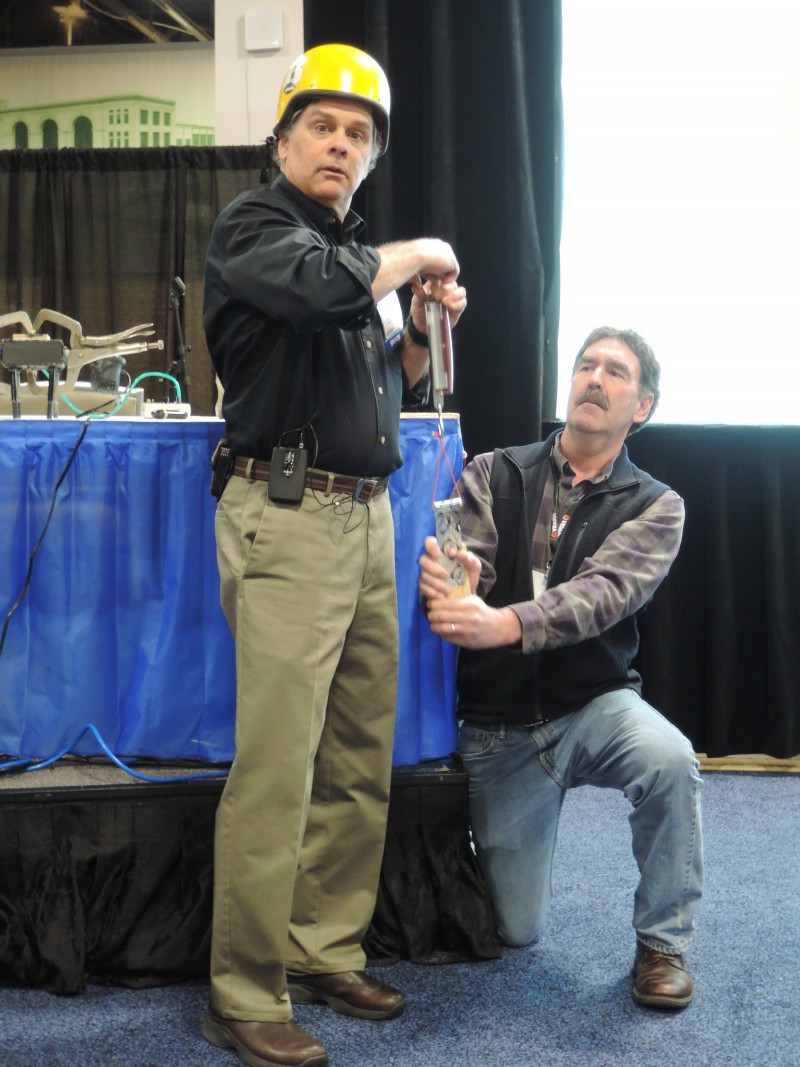
Round Two: ASTM D3654 – Method A
More than one PSA tape test manufacturer told us that ASTM D3654 – Method A was the best tension test to use.
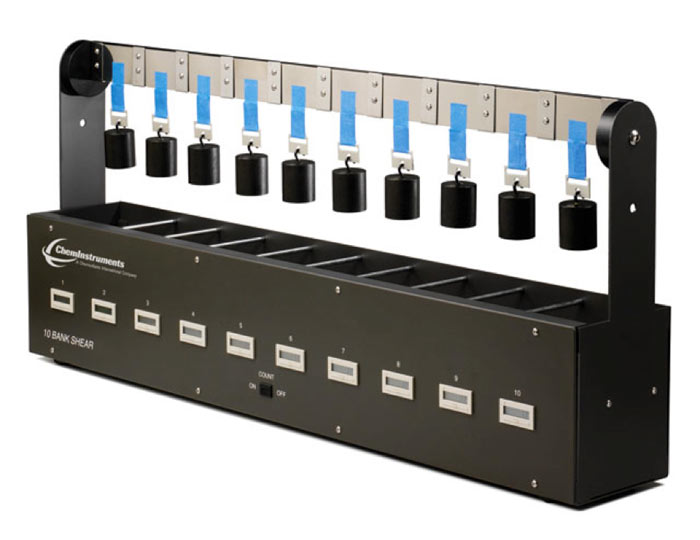
We tested about a half dozen tapes on about the same number of substrates under two application conditions: warm-dry and cold-damp. After application (none of which used any primer, by the way), all testing was done outdoors, with the testing sheltered from wind and UV but exposed to outdoor temperatures and relative humidity. We started this round of testing on December 2, 2013 (and it will continue for at least one year to move the tests through a full range of outdoor exposure). Our selection of tapes and substrates was driven in no small part by what products and applications our SEON high-performance building guild wanted to see us test.
It’s now been more than 90 days, and we have results we are willing to share (download the Excel spreadsheet). The spreadsheet results are set up by key days—1, 3, 7, 21, 45, and 90. There are a LOT of results, and they can be pretty dense, so here is a summary.
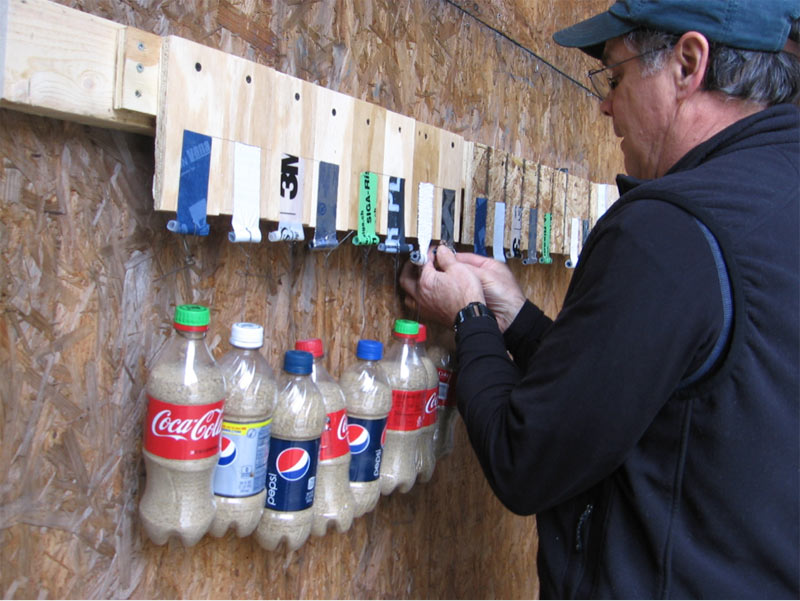
- We have not (yet) seen much of a pattern favoring warm-dry application of tapes to substrates; at day 90 days, there were an equal number of tape failures for each condition. That’s a bit of a surprise, frankly.
- Quite a few tapes on rough OSB let go within the first week.
- A broad range of tapes are performing well on rigid insulation: XPS and foil-faced polyiso.
- Some tapes have expressed “creep;” the 1 kilogram weight is enough of a load to cause the entire tape to slip down from its original 3-inch contact area with the substrate.
- The “solid” acrylic tapes (Pro Clima and Siga) are performing well regardless of conditions and substrates. (These are tapes we approve in our collection.)
- The two butyl tapes (Pella and FlexWrap) have struggled with the wood substrates and are giving mixed results so far on the two rigid insulations.
- Vycor (modified bitumen) performed poorly on wood substrates but has performed well to date, regardless of conditions, on the XPS and foil facing
Round Two Caveats & Test Changes
Dave and I feel we made some mistakes in this round of testing.
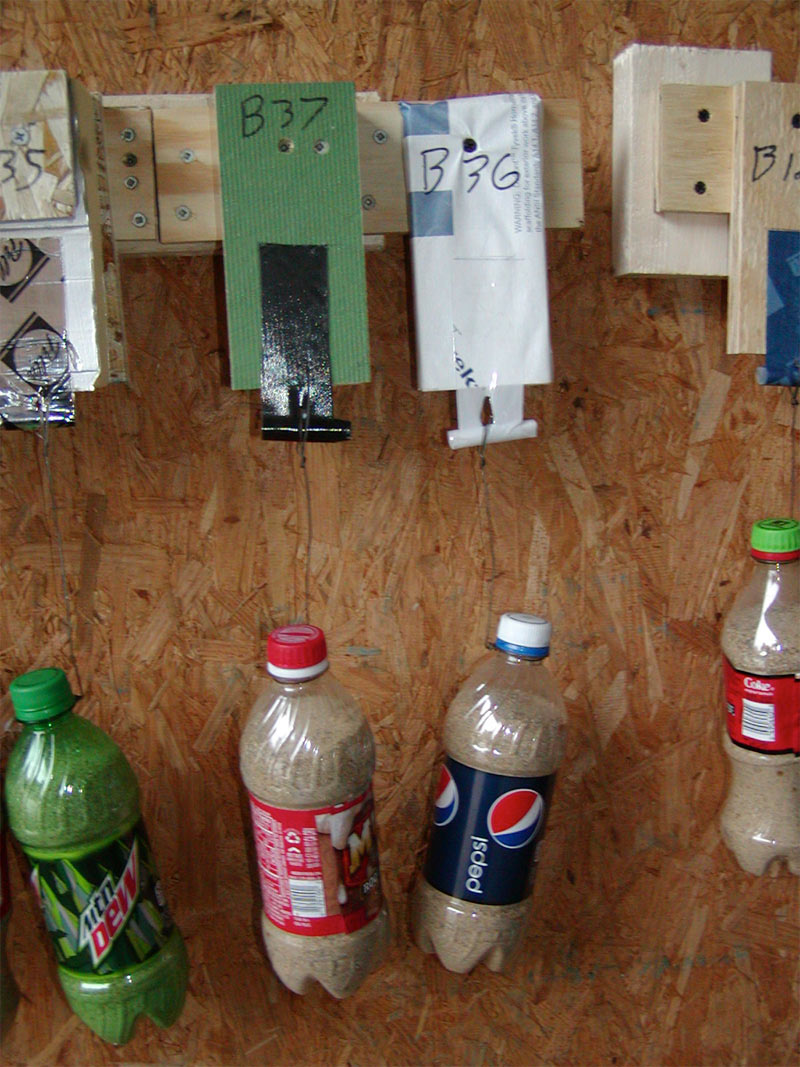
- While we chose a full kilogram to “force” differences among the tapes, it does seem to be a bit of an overload, especially for tapes designed to give or stretch.
- Hanging the weights by way of a wire puncturing the tape has resulted in tape tear failures that, while interesting in and of themselves, mean that we lost the opportunity to compare those tape adhesives (all four tape tears were Pella and Tyvek tapes).
- We used a Siga tape supplied by one of our SEON builders that turned out to be an interior tape. Oops.
- Our SEON builders and architects really wanted to see popular tapes, such as Tyvek and ZIP, tested on a wide variety of substrates, not just the ones for which they were designed.
In February 2014, WTF started a new round of “ASTM D3654 – Method A-like” testing. We’re going to look at Pella, OC FlashSeal IR, Tyvek, Siga Wigluv, and ZIP tapes on four substrates: rough OSB, Tyvek housewrap, XPS, and foil-faced polyiso (Our SEON builders and architects really wanted to see popular tapes, such as Tyvek and ZIP, tested on a wide variety of substrates, not just the ones for which they were designed). Fixing our mistake with the weights, we’re coming down to one-pound weights, and a new clip attachment that won’t produce the same stress. We’re testing with cold-damp application and damp-warm tempering.
NOTE: It may look as though we are missing the Pro Clima Tescon Vana and some other high-performing tapes/substrates with this new round of testing, but the “older” test lives on, and these tapes just don’t seem to mind the puncture-loading and greater weight.
Stay tuned for end-of-summer results on this new testing.
Round Three: “Bellowing” and the WTF Pressure Pig
In addition to temperature and moisture-content changes that can stress the tapes and their adhesive bonds to substrates, wind can make elements of any exterior barrier system—like sheet goods and tapes—bellow back and forth with positive and negative pressure cycling.
Dave and I wanted to make some sort of WTF rig to simulate this sort of tape stress. So one of Dave’s more creative guys at his SIP plant made up the WTF Pressure Pig.
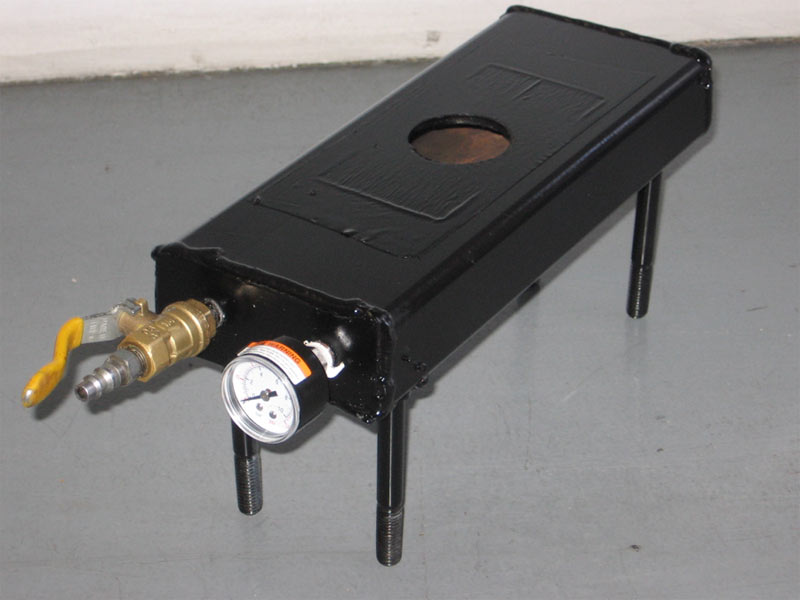
We took a piece of OSB as the substrate, kerfed out a strong eighth-inch slot, and then adhered a piece of PSA tape.
Then we added pressure to the nozzle and read the pressure as the tape bulged and eventually—at about 3 pounds per square inch (PSI)—peeled and leaked air. We scratched our heads and wondered what relationship 3 psi had to the pressures a building enclosure might see.
Holy Smokes did we get dope-slapped!
1.0 pounds per square inch (psi) = 6984.7 pascals (Pa)
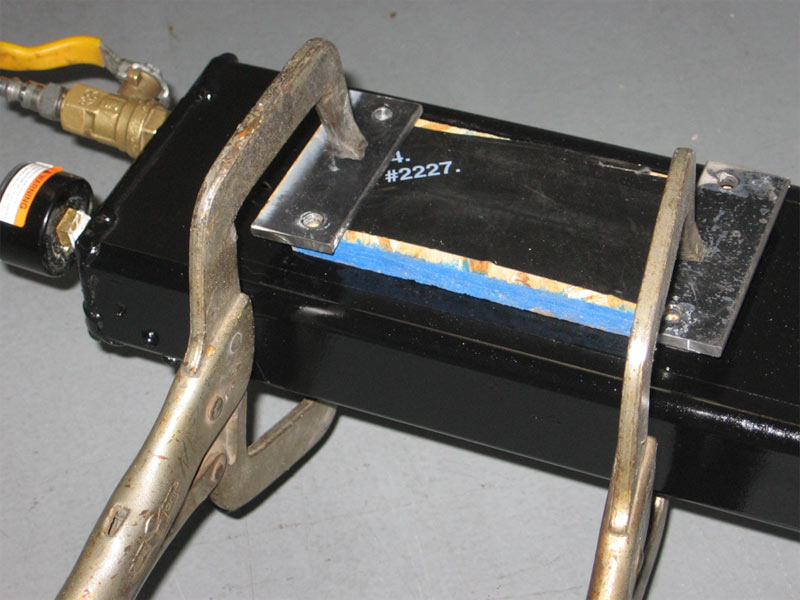
Three psi is what you might expect a building to experience at ground-zero in an F4 tornado or a Category 5 hurricane. PSA tape failure at that point is not the central problem…
So, we decided that modifying the WTF Pressure Pig to exert pressure somewhere in the range of a blower door test (50 Pascals) or an air barrier test (75 Pa) made a ton more sense. Dave cleverly rigged up an air mattress pump to the Pressure Pig, and we switched out the 120 psi capacity pressure gauge for an Energy Conservatory digital pressure gauge (maximum capacity of 2,000 Pa). And when Dave re-piped the Pressure Pig, he had the air flow set perpendicular to the pressure inlet so that varying the bleed valve moved the pressure from positive to negative—voila, bellowing (based on the Bernoulli principle).
Time for dope-slap number two: at even just ±100 or so Pa, ANY tape on ANY substrate is barely stressed at all, at least that we could observe with a series of 10 pressure cycles or bellowing events. What does this mean for Round Three testing?
We think it means one of two things: either we really don’t need to worry about the stress bellowing places under real conditions on real buildings, or, we need to set the WTF Pressure Pig to cycle many hundreds of times over the course of a MUCH longer time frame, OUTDOORS, to reveal the real nature of the stress and possibly differentiate tape performance in this way. Looks as though we will be hitting up WTF research underwriters real soon, either Coke or Pepsi or actual building product manufacturers who make tapes and substrates.
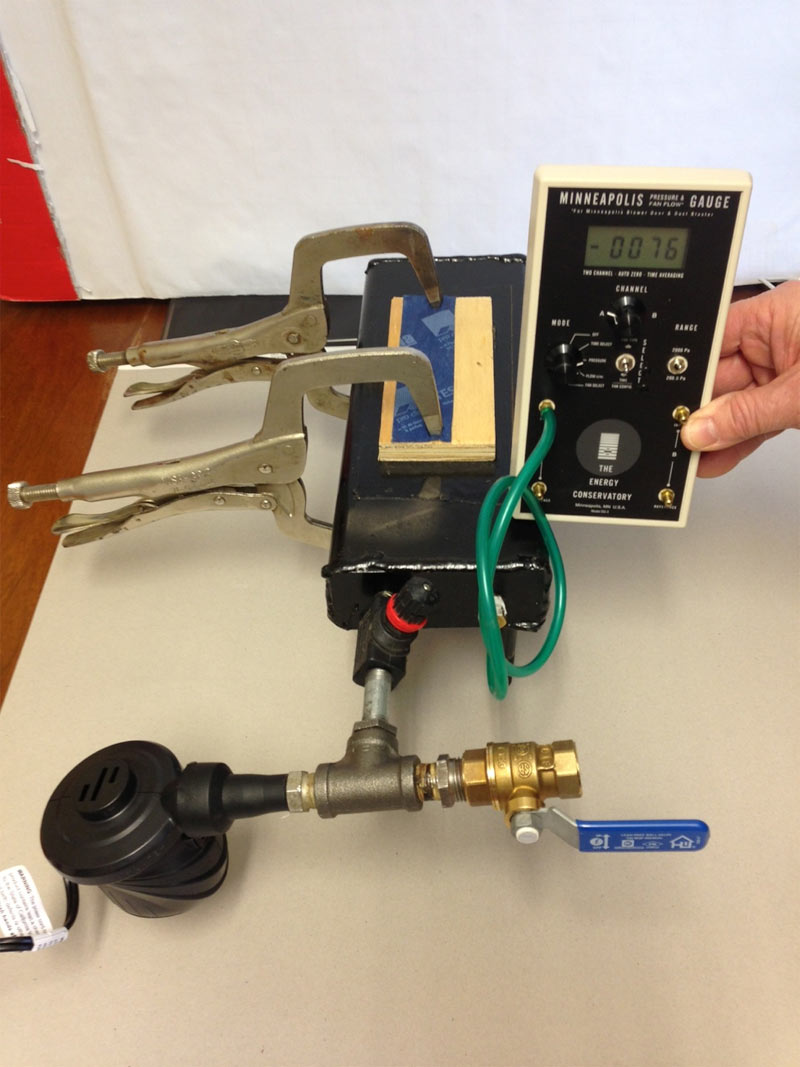