A research engineer at Pella Windows finally offers some adult supervision for our benchtop tape tests.
When the Wingnut Test Facility (WTF) took its tape testing protocols on the road, as I reported in my last post, a stranger stepped forward to politely offer some “adult supervision.”
It’s true that there aren’t any industry standards for testing tapes in dirty, wet, or cold conditions, says Jaron Vos, a research and field engineer for Pella Corp. That doesn’t mean manufacturers are ignoring the issue.
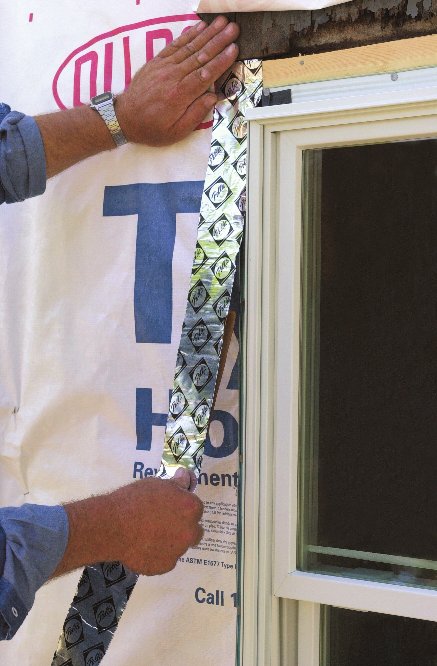
Welcome to the real world
According to Vos, in 2001 when Pella was developing its SmartFlash Tape, the company’s researchers focused on conditions they thought the tape would encounter during real use by real installers. They tried to replicate those conditions in the lab and got feedback from installers.
“It’s not that ASTM and similar test standards are not useful,” though, says Vos. “In fact, we used AAMA’s 711 extensively for measuring performance after trying to replicate jobsite or service life conditions.”
AAMA 711
AAMA 711, Voluntary Specification for Self-Adhering Flashing Used for Installation of Exterior Fenestration Products, is a pretty comprehensive set of minimum requirements for pressure-sensitive adhesive (PSA) tape performance.
Vos relates, “We tested a number of adhesives and backing options in an approach similar to AAMA 711 (although during initial Pella testing, AAMA 711 was not yet available). While it is difficult to say how many years of service life is simulated by any one of these tests, or how many other conditions we could try to simulate, we certainly spent some time and effort evaluating PSA tape materials.”
Pella’s four tips for flashing tapes
Vos shared several findings with us:
- Kiss your asphalt goodbye. Vos: “We found that the asphalt tapes performed poorly in the extreme temperatures and reacted poorly with sealants.”
- Acrylic can’t take the heat. “The acrylic tapes we tested were either too thin to self-heal or too thick and runny at high temperatures,” said Vos. NOTE: Vos did not test any of the high-end, solid acrylic tapes, such as Siga or Pro Clima tapes that we include in our BuildingGreen Approved collection.
- Watch your backing. “We also found that any tape with a mylar or polyethylene backing could not protect the adhesive from UV damage,” explains Vos. “Those materials also require a knife or scissors to cut and have varying amounts of ‘memory’ (they tend to pull the adhesive back from places you try to put it). Tapes that were too thick or have textured backing could create leak paths at their overlaps and unwanted material buildup. Tapes that were too thin couldn’t self-heal around fasteners.”
- Rubber gets a bounce. This explains why the Pella SmartFlash tape ended up using a butyl rubber adhesive and aluminum foil backing: Pella asserts that its SmartFlash tape works well in both hot and cold, that its backing is UV resistant, and that the tape offers good sealing around tape penetrations. The tape is also designed to tear by hand, simplifying things on the jobsite and potentially reducing labor costs.
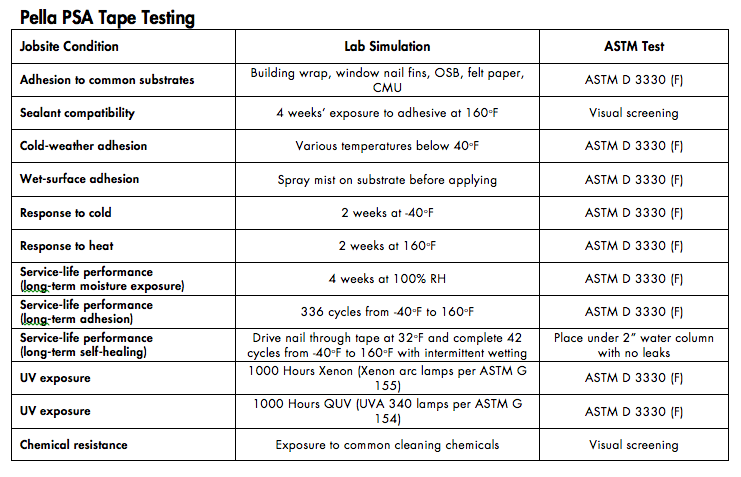
We still need better tests
It’s nice to have some additional perspective on this whole issue of PSA tape performance, but back at WTF’s underground laboratories, Dave and I have been cooking up two new tests: one that mimics the “bellowing” effect of wind pressure pushing in and out on the tapes and another that represents the shear that takes place across the tapes when they are stressed by movement of building components.
We’ll let you know as soon as we’ve made some progress on this more complex testing approach.